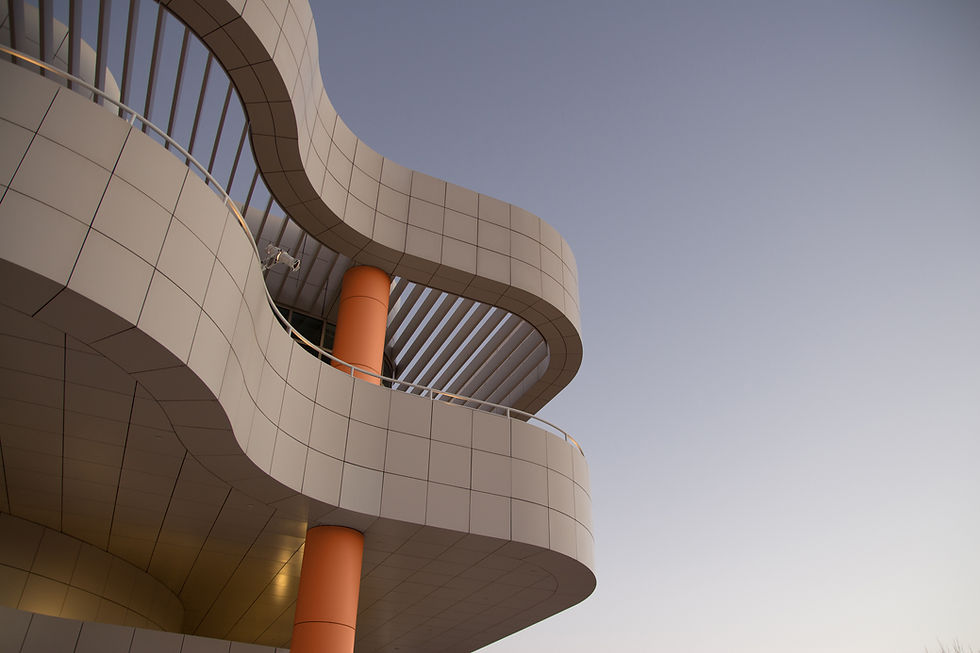
Scaling Framework in Low-Volume, High-Complexity Manufacturing
Oct 7, 2024
5 min read
Low-volume, high-complexity (LV/HC) manufacturing presents unique challenges, especially when facing unpredictable economic shifts and fluctuating market demands. As original equipment manufacturers (OEMs) encounter increased product complexity, extensive customisation requests, and persistent supply chain disruptions, they must adapt their sales and operations planning (S&OP) strategies. This blog delves into key strategies for improving S&OP in this complex environment, offering actionable insights for industry experts and middle managers in the manufacturing sector.
LV/HC products are often substantial in size or of a unique specification/nature - think of power transformers, offshore drilling platforms, large-scale wind turbines, mine shaft winder bearings, or custom-made bicycles - and are typically crucial to a customer's operations. Their high prices reflect the complexity of their components, rigorous quality requirements, customised production intricacies, and the need for expansive manufacturing facilities with specialised machinery. Labour costs also tend to be significant, as automation is less prevalent in such complex production processes.
Since automation isn't a viable option for driving efficiency and streamlining in LV/HC manufacturing facilities, scaling requires a more nuanced approach. We'll explore a six-pillar framework designed specifically to support the growth and optimisation of these complex manufacturing operations.
The framework can be downloaded below.
It's crucial to always align with the overall business strategy, as this overarching plan determines the priorities and emphasis of each pillar. The strategy serves as a guiding force, ensuring that efforts are focused on the areas most critical for success.
Sales and Operations Planning (S&OP)
Forecasting LV/HC product demand is no easy task, as unexpected economic shifts can have a significant impact on orders. When dealing with a small customer base, an inaccurate forecast can lead to costly overproduction or missed opportunities. Unfortunately, many OEMs have not updated their demand or capacity-planning strategies, making it difficult to manage the increased complexity and uncertainty.
Key Takeaways for Improved S&OP:
Data-Driven Decision Making: OEMs should base demand and capacity planning on hard data and statistical analysis from both internal teams and external suppliers. This approach requires filling data gaps and ensuring that data quality remains high, especially in areas with the most value at stake.
Resilience Planning: Include a resilience component in your plans to handle potential disruptions, such as workforce shortages or supply chain delays. Identify potential disruptions in advance and create business rules for appropriate responses, such as nearshoring production or adjusting inventory levels.
Integrated Value Chain Planning: Develop comprehensive plans for all activities along the value chain, including material ordering, production line scheduling, and supplier requirements. Use cloud-based systems to make planning documents accessible to stakeholders across the value chain and create transparent information and management.
By consolidating all information into a master plan with clear insights, results, and task ownership, OEMs can improve transparency, reduce the need for frequent replanning, and provide frontline workers with consistent guidance.
Managing Supply Chain Disruptions
The global nature of LV/HC product manufacturing often means that supply chain disruptions are inevitable. When a single component is delayed, it can cause serious ripple effects across the production process.
Strategies to Manage Supply Chain Disruptions:
Supplier Performance Tracking: Implement dashboards to monitor key performance indicators (KPIs) for each supplier. Consistent communication and accurate data entry will help detect problems early, enabling joint problem-solving sessions and transparent sharing of information.
Integrated Finances: Streamline payment processes by integrating purchasing and accounts payable databases, expediting transactions and ensuring suppliers remain committed to your supply chain.
Parts Transparency: Adopt systems to track the exact location of critical parts throughout production, reducing the risk of shortages and minimising production disruptions.
Centralised Quality Audits: Maintain a central database with quality audit information to avoid redundant checks and improve the overall quality of parts received from suppliers.
By proactively managing supply chain relationships, OEMs can minimise disruptions and maintain production momentum.
Optimising Inventory Management
LV/HC product OEMs often face inventory challenges due to outdated guidelines that don’t reflect current realities, such as increased supply chain disruptions and longer lead times.
Optimising Inventory for LV/HC Manufacturing:
Update Inventory Guidelines: Regularly review and update inventory guidelines, accounting for supply chain shifts and transportation changes that might affect lead times.
End-to-end Transparency: Implement real-time monitoring of inventory levels and collaborate closely with suppliers to manage vendor inventory levels effectively.
Reduce Safety Stock Buffers: Gain insights into supply needs by ensuring end-to-end transparency, which helps reduce unnecessary safety stock and optimises material flow.
Establishing stronger relationships with suppliers and enforcing schedule adherence can further enhance inventory management.
Enhancing Shop Floor Efficiency
LV/HC product shop floors are often characterised by multiple specialised teams working simultaneously on different projects, making it difficult to pinpoint issues such as disruptions, parts shortages, and quality problems.
Strategies for Efficient Shop Floor Management:
Digital Documentation: Implement clear and consistent digital documentation using standard defect codes, enabling better tracking and problem-solving.
Autonomous, Multifunctional Teams: Empower teams to prioritise tasks and allocate resources independently, reducing disruptions and increasing employee satisfaction.
Automated Visual Inspections: Incorporate additional checking and testing processes, such as automated visual inspections, to catch potential issues early and minimise disruptions.
Creating a culture of ownership and responsibility on the shop floor can lead to improved efficiency and reduced production disruptions.
Building a Strong and Loyal Workforce
Labour shortages present a significant challenge for LV/HC OEMs, especially as many skilled workers approach retirement age. Talent retention is critical to managing ramp-ups and maintaining production efficiency.
Key Workforce Strategies:
Advancement and Clear Career Paths: Offer clear pathways for career growth and rapid advancement, especially for younger workers who value progression opportunities.
Flexible Work Arrangements: Consider flexible work schedules and hybrid work options to attract and retain talent in a competitive market.
Talent “Win Room”: Create a temporary talent “win room” to streamline recruitment, retention, and training processes, ensuring a steady supply of skilled labour during ramp-ups.
Investing in workforce development and creating a positive work environment can help OEMs retain skilled employees and maintain production momentum.
Implementing Effective Change Management
To facilitate successful ramp-ups, OEMs must address cultural and organisational challenges, particularly around accountability and decision-making.
Change Management Best Practices:
Clear Roles and Responsibilities: Create multifunctional teams with well-defined roles, responsibilities, and KPIs to ensure that every team member understands their contributions.
Autonomous Decision-Making: Empower teams to make decisions independently, reducing bureaucracy and enabling faster problem resolution.
Escalation Guidelines: Establish clear guidelines for escalating issues, ensuring that only critical matters reach senior leadership, allowing them to focus on strategic priorities.
Effective change management ensures that OEMs can adapt to evolving challenges, maintain efficiency, and achieve ramp-up success.
Our Responsibility Beyond Our Walls
Although our primary focus has been on OEMs, these strategies can be just as impactful for other players in the value chain, like suppliers and raw material providers. When everyone works together and embraces similar approaches, the entire ecosystem stands to gain from enhanced production efficiency and ramp-up success.
For example, smaller suppliers, by adopting flexible work arrangements and offering clear career paths, can attract and retain talent much like their larger OEM counterparts. Additionally, suppliers who invest in better supply chain practices can significantly reduce delays, positioning themselves to meet increased demand more effectively as OEMs ramp up production. This collaborative mindset ultimately ensures smoother operations and shared success across the value chain.
LV/HC OEMs and their partners face a rapidly evolving landscape where product complexity, supply chain disruptions, and workforce challenges are the new norm. By embracing data-driven planning, resilient supply chain management, efficient shop floor practices, and a strong workforce culture, manufacturers can not only survive but thrive in this uncertain environment.
As demand for LV/HC products continues to rise, the urgency for implementing these strategies will only grow, making it essential for manufacturing professionals to act now.
If you're looking for guidance on any of these areas to enhance your business operations, feel free to connect with us. Let's explore how we can contribute to your strategic success.
Subscribe to our Newsletter.